Brownfield warehouse: 7 key steps to automating your warehouse
April 29, 2024
For many businesses, the key to maximising efficiency lies in automation. However, transitioning a brownfield warehouse, one that is already in operation, to an automated system can be a daunting task. With the right strategy and approach, it can be a seamless and rewarding process.
In this guide, we’ll explore the essential steps to automating your brownfield warehouse, ensuring a smooth transition and maximising the benefits of automation.
1. Assess your current processes
The initial step is to have a profound understanding of your business operations, identifying areas where inefficiencies or gaps exist. By comprehending day-to-day operations and pinpointing where processes may be lagging, you can then explore how robotics and automation can be integrated to address and bridge these gaps effectively.
When your business doesn't currently face glaring issues, the next consideration is how to elevate your performance and seize opportunities for improvement. Robotics and automation can play a pivotal role not just in troubleshooting but also in enhancing overall efficiency.
Conduct a thorough assessment to identify bottlenecks, inefficiencies, and areas ripe for improvement. This step is essential for understanding the unique needs and challenges of your brownfield warehouse.
Utilise data analytics tools to gather insights into inventory movement, order processing times, and resource utilisation. By gaining a comprehensive understanding of your warehouse operations, you can pinpoint areas where automation can make the most significant impact.
For example, let’s say a distribution company that supplies electronic goods to retailers. This company has been using a traditional warehouse management system for years, but as their business grows, they start experiencing challenges such as delayed order processing, inventory discrepancies, and inefficient use of warehouse space.
To conduct an assessment of their current processes, the company uses data analytics tools and they gather data on various aspects of their warehouse operations, including:
- Inventory movement: They track the flow of inventory within the warehouse, analysing which items are frequently picked and shipped and which ones remain stagnant on shelves.
- Order processing times: They measure the time it takes from receiving an order to picking, packing, and shipping it to customers.
- Resource utilisation: They assess the utilisation of equipment (such as forklifts and conveyors) and manpower to understand if there are any inefficiencies or underutilised resources.
During this assessment, the company can discover areas for improvement such as noticing that manual data entry errors are causing discrepancies between physical inventory counts and system records.
Based on these findings, the company identifies specific areas where automation can make a significant impact. For example, introducing barcode scanning technology to minimise manual data entry errors and inventory accuracy.
2. Set clear objectives
With a solid understanding of your current processes in hand, the next step is to define clear objectives for automation. What are your overarching goals? Whether it’s reducing labour costs, increasing throughput, improving accuracy, or enhancing customer satisfaction, setting specific, measurable, achievable, relevant, and time-bound (SMART) objectives is essential. These objectives will serve as a roadmap for your automation efforts, guiding decision-making and ensuring alignment with your business goals.
For example, if you are a retail company - after assessing your current processes - you can identify several goals such as:
- Reducing labour costs: Decrease labour costs associated with manual tasks such as picking, packing, and inventory management. By automating these processes, you can reallocate resources more efficiently.
- Improving inventory accuracy: Another key objective could be to improve inventory accuracy and reduce errors in order processing. Manual data entry errors and discrepancies between physical inventory counts and system records have been causing delays and customer dissatisfaction. By adopting automated inventory management systems with barcode scanning, you aim to enhance accuracy and minimise errors.
- Enhancing customer satisfaction: You can do so by providing faster order processing, accurate inventory information, and timely delivery.
3. Choose the right technology for your needs
Selecting the appropriate technology is key to the success of your automation initiative. With plenty of options available, ranging from robotic systems to warehouse management software (WMS), it’s crucial to choose solutions that align with your objectives and integrate seamlessly with your existing infrastructure.
Consider factors such as scalability, compatibility, ease of implementation, and total cost of ownership when evaluating technology vendors. Collaborating with industry experts and seeking recommendations from peers can help narrow down your options and ensure you make informed decisions.
For instance, a pharmaceutical company, facing challenges with inventory accuracy and slow processing times, recognises the need for a technology that can provide real-time visibility of their inventory and warehouse operations while improving accuracy and efficiency. In this case, Dexory's system promises to scan up to 10,000 locations an hour and achieve 99.9% inventory accuracy, significantly enhancing the company's inventory management capabilities.
4. Implement the incremental changes
Attempting to automate your entire warehouse in one fell swoop can be overwhelming and risky. Instead, adopt a phased approach by implementing incremental changes.
Start small, focusing on one area or process at a time, and gradually expand automation efforts as you gain confidence and experience. This approach allows you to mitigate risks, minimise disruptions to ongoing operations, and demonstrate tangible results early on.
Additionally, soliciting feedback from warehouse staff throughout the implementation process fosters a culture of collaboration and ensures buy-in from key stakeholders.
5. Enhance your operation while keeping it running smoothly
While you implement a new technology in your warehouse operations, it’s essential to install it while the distribution business continues to operate. Here are several considerations for planning a warehouse brownfield automation project:
- Facility modifications: If construction or modifications of your facility are required for implementing the new solution, provide information to your partner regarding the floor flatness, warehouse hygiene, load management or electrical details.
- Documentation: Provide your partners with current electrical, mechanical and control details to ensure a smoother integration process.
- Implementation planning: Supply your partner with a plan on how they can navigate the existing operation - during operational and non-operational hours - and assess the impact of operational changes.
- Occupied space: Allocate a space within your facility for your partner team to be able to work and integrate the new solution.
6. Communication, training and upskilling employees
While automation promises to streamline operations and boost efficiency, it’s essential to recognise that it also necessitates a shift in workforce dynamics. As such, investing in training and upskilling programs for your employees is critical.
- Provide comprehensive training on new technologies and processes, equipping your workforce with the skills and knowledge needed to thrive in an automated environment.
- Organise a dedicated day for the team to understand the technology, learn its benefits, engage with it, and personalise the experience by choosing a name for the robot for example. This approach fosters confidence and investment in the automation process, leading to successful implementation.
- Encourage continuous learning and professional development to ensure that your team remains adaptable and resilient in the face of change.
By empowering your employees, you not only enhance productivity but also foster a positive work culture centred around growth and innovation.
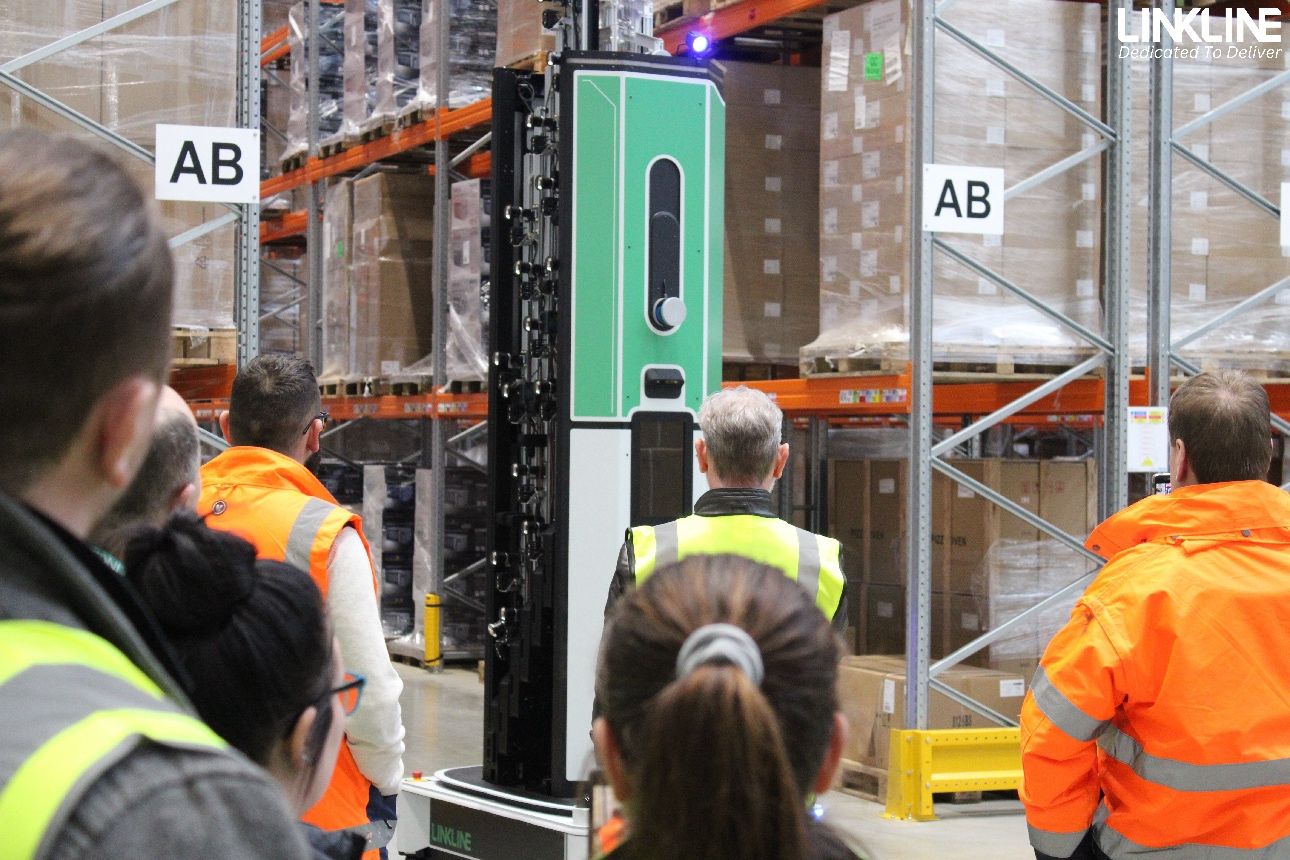
7. Monitoring and continuous improvement
The journey to automation doesn’t end once your brownfield warehouse is up and running smoothly. In fact, it’s just the beginning. To maintain a competitive edge and drive ongoing improvements, it’s crucial to establish robust monitoring and continuous improvement mechanisms.
Leverage real-time data analytics to track key performance indicators (KPIs) and identify areas for optimisation. Regularly review processes, solicit feedback from stakeholders, and iterate on your automation strategy accordingly.
Dexory can help
About us
By partnering with Dexory on your warehouse automation project, you will work with a team of experts in logistics, robotics and data insights who have managed and integrated numerous implementations. With our dedicated testing and development warehouse, we guarantee the robustness of our products before they reach your site.
Enjoy 24/7 global support, minimising disruptions and ensuring smooth operations across all time zones. Through predictive maintenance and ongoing monitoring, we proactively address any issues, keeping your systems running optimally.
We prioritise collaboration with your teams, empowering them to leverage the full potential of the data packages collected — putting your people first!
About the solution
DexoryView AI-powered platform combines the use of autonomous robots to scan warehouses up to 1 million sq ft plus and over 100,000 pallets in a day, providing accurate, instant, real-time information on goods and assets across the sites it operates in.
Leveraging AI algorithms, alongside the use of enhanced sensors across Dexory’s robots, DexoryView will now power logistics teams with accelerated time to insight and action to make better data-driven informed decisions on operations, expanding outside of inventory.
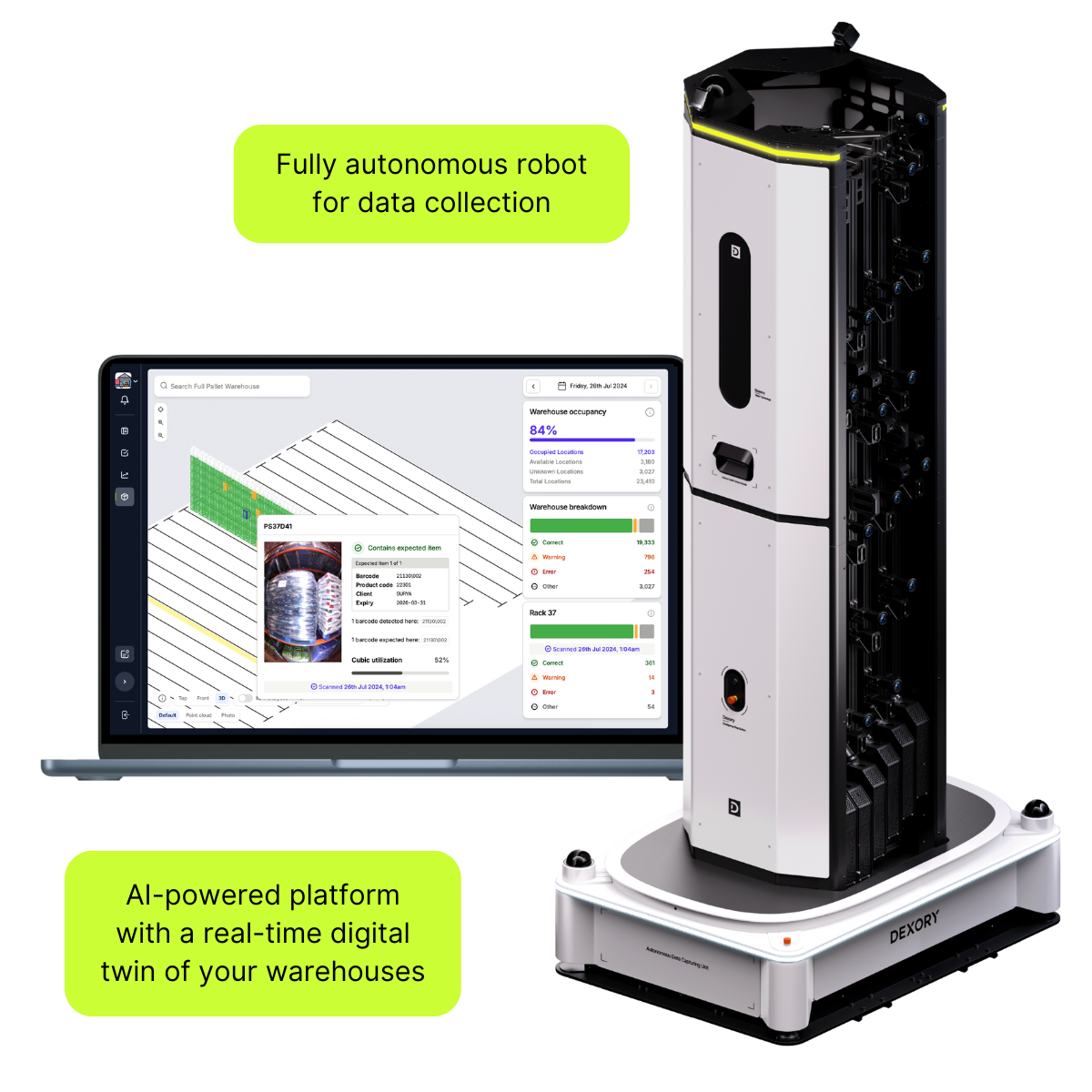
Conclusion
Automating your brownfield warehouse is a transformative journey that requires careful planning, strategic execution, and a commitment to continuous improvement. By following these essential steps, you can unlock the full potential of automation, streamline your operations, and position your business for long-term success.
Remember, the key lies in assessing your current processes, setting clear objectives, choosing the right technology, implementing incremental changes, investing in employee training, and embracing a culture of continuous improvement.