How Dexory’s inventory management robots work
February 20, 2024
The rise of goods
The volume of goods moving across the globe is now higher than ever before and is expected to continue rising exponentially. By 2050, the amount of freight transported by sea is predicted to reach 250 billion tonne kms, which is four times higher than in 2010. While road freight is set to increase by 380% and rail freight by 350% [1].
This has triggered the need for larger warehouses, as companies hunt for more space. In the UK, the average size of unit has increased from 217,000 sqft (20,000 m²) in 2015 to 340,000 sqft (31,500 m²) in 2020. The average eaves height has also risen from 11 m to 14 m [2].
However, these larger warehouses present new challenges to warehouse managers, particularly with inventory stock taking and operational visibility. To keep track of the higher volume of goods, warehouses now need to audit more pallets per hour and reach racks that can be up to 14 m tall.
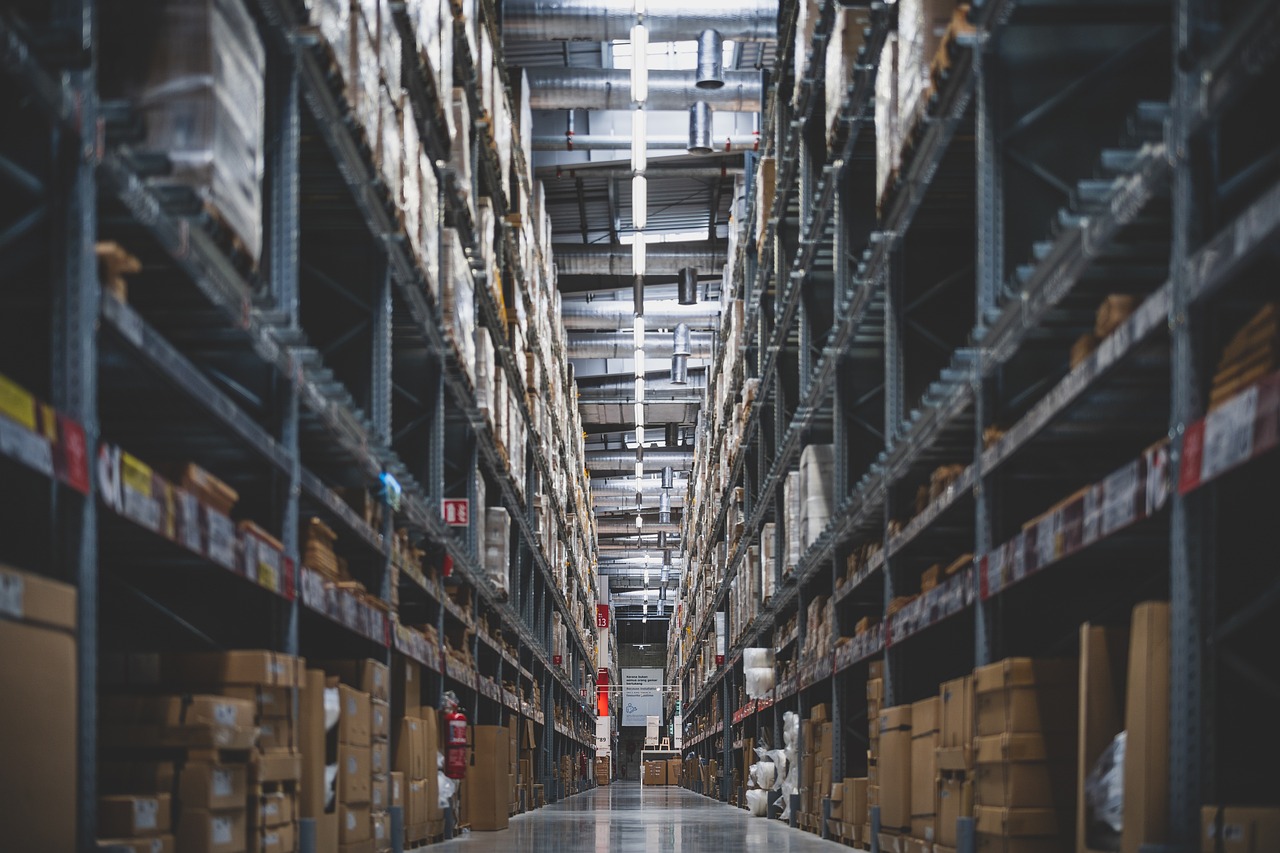
Warehouse automation benefits
Typically, a stock take involves manually scanning, which requires lifting human workers by forklift to reach the top of racks. This not only raises safety concerns but is also time consuming, resulting in less than 100 pallets scanned per hour, on average.
Alternatively, drones mounted with cameras can be used which can reach the tallest racks with ease and can scan 400 pallets per hour. However, drones often suffer from scanning inaccuracies, they require human operators control and also aisles need to be closed for safety during scanning.
To solve this problem, Dexory used Autonomous Mobile Robot (AMR) technology to develop an inventory management robot that automatically extends to the height of the tallest racks. It uses both lidars and cameras to scan every pallet within a rack simultaneously, in one sweep; scanning up to an impressive 12,000 pallets per hour with an average well above 8,000 pallets and an accuracy of 99.9%.
Consequently, warehouses can be scanned every day, regardless of its shape or size. This data is then integrated into a digital twin platform called DexoryView which provides warehouse managers with real time visibility of every location in their warehouse or warehouse network.
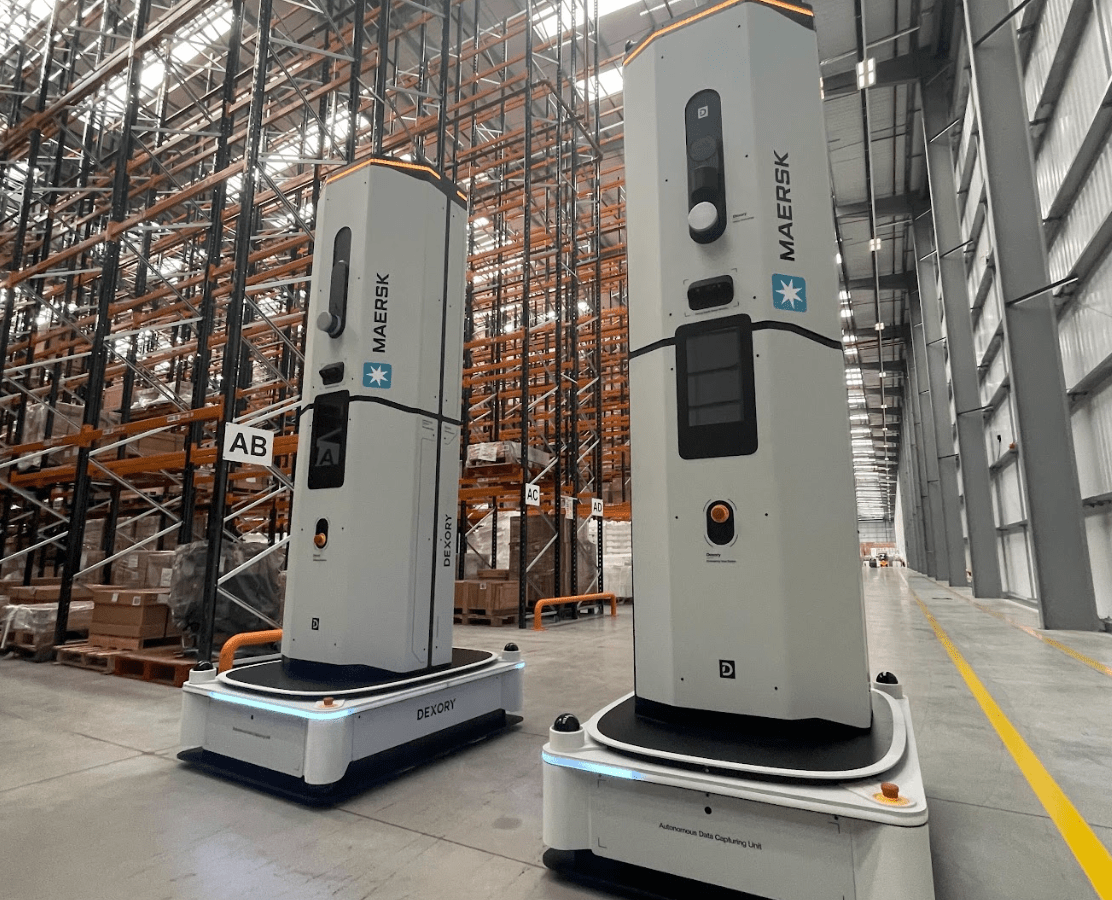
Dexory helped logistics giant Maersk increase its warehouse scans from once every two weeks to daily or even multiple times a day.
The extendable tower technique
‘The first question we asked ourselves was how tall does the inventory robot's tower need to be?’ explains Peter Bushell, Design Engineer at Dexory. ‘The maximum height of the warehouses we were targeting at the time were 14 m. We then looked at the minimum height which was dictated by practical factors, as we wanted to collapse the robot down to a manageable height for manufacture, transportation and assembly.’
‘In the end, we opted for a tower with a minimum height of 3 m that could extend to 12 m, with a camera at the top to measure racks of 14 m. Once we had the minimum and maximum heights defined, we then had to develop a mechanism that allowed the robot to actuate between these two heights. That’s when the real challenge began.’
The tower essentially extends and collapses like a telescope. It has multiple lifting sections that are mechanically linked. Each section is made from an aluminium frame with a triangular cross section which gets progressively smaller as you move up the tower. This allows the lifting sections to support each other when extended, but also nest within each other when collapsed down.
Dexory’s tower extends and collapses like a telescope, allowing it to accurately scan pallets at full rack height.
‘We decided to go for a triangular cross section because this meant a significant weight reduction compared to a square,’ says Bushell. ‘These triangles are made up of extruded aluminium profiles and we’ve designed the structure so that the point of each triangle also acts as a guide for the runners. That’s the other nice thing about triangles, they are extremely rigid, light and can self-align when the tower extends.’
Integrating the scanning system
Once the tower is at full height, it needs camera’s, lights and lidars mounted at specific points to scan each row within a rack. However, with the core lifting structure so densely packed, there was no space left to mount these directly to the lifting sections.
Instead, a separate scanning rail was designed. This not only mounted all the relevant scanning systems, but also housed the necessary cabling and electronics. ‘Each scanning rail connects to the top of its corresponding lifting section. So when each section lifts, so does the relevant scanning rail,’ explains Bushell.
‘One of the most difficult challenges we had was actually managing all the cabling,’ continues Bushell. ‘There are a total of 17 cameras, 17 lights mounted to the scanning rails with two lidars, all of which require a power and data connection.'
'We had to find a way to connect a camera 12 m in the air with a computer in the base,' says Bushell. 'These cables also had to cope with transferring large volumes of data whilst constantly being extended and collapsed as the scanning rails move.’
The approach was to locate small computers at the bottom of each scanning rail to locally process the data. This meant the cables only needed to be as long as the scanning rail and therefore did not need to bend. It also enabled the use of more robust cables, which improved the reliability of data transfer.
‘All of these computers are linked to the base by a network of ethernet cables which are much more robust and can cope with bending,’ says Bushell. ‘We’ve housed these in plastic drag chains which help to control the motion of the cables as the sections move up and down.’
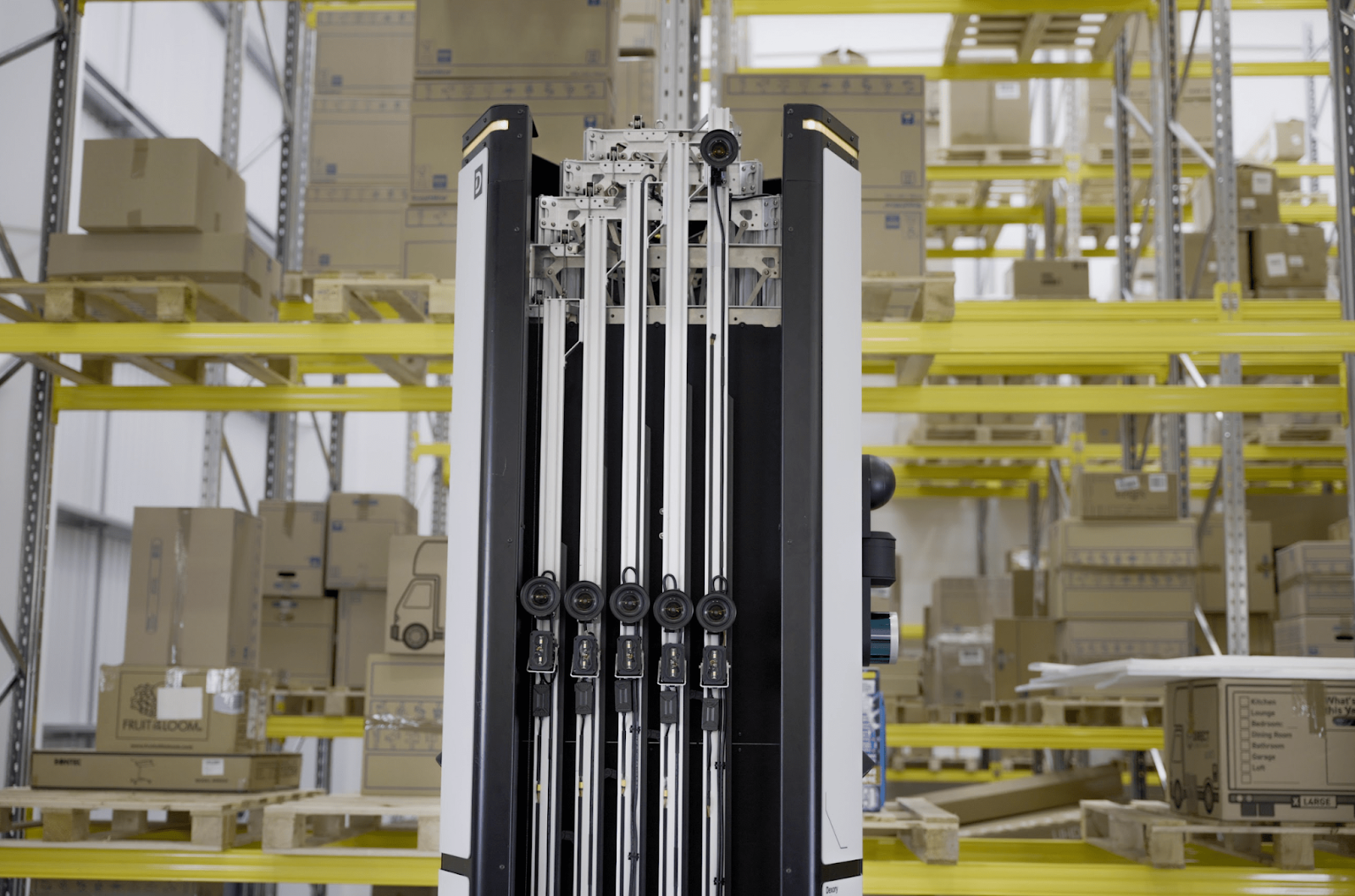
Each of the six lifting sections has a corresponding scanning rail that mounts camera’s and lights, with two lidars located at the top of lifting sections 3 and 5.
Actuating the tower
Mechanically lifting the tower presented another technical challenge. The sections needed to lift simultaneously but as each section targets a different height, they all had to lift at different speeds. This was achieved with a complex rope and pulley system at each corner of the tower, powered by a winch.
‘Our design moves the pulley, not the end of the rope which allows us to effectively double the speed of each section,’ says Bushell. ‘So as one section lifts up, it takes the next section with it, which moves twice as fast. This pattern repeats until the tower reaches its full height.’
Moving these sections smoothly and evenly past each other requires an effective sliding mechanism that achieves minimal friction but remains rigid. To solve this, the engineers at Dexory decided to develop linear bearings using sliders made from Ultra High Molecular Weight Polyethylene (UHMWPE) plastic which has an extremely low coefficient of friction.

Low friction sliders are mounted to the aluminium frame at specific points to help keep the lifting sections in place whilst facilitating movement.
Another problem Dexory had to overcome was the bending of the tower. A 12 m tall structure with measuring equipment mounted on one side will always bend because nothing is infinitely stiff.
To minimise this bending, Dexory took a different approach and assumed that the tower is always at a slight angle. Consequently, this leads to different design assumptions as we were no longer considering vertical forces and instead only the considering bending moments needed to be considered and the relevant. This meant we could pinpoint the linear bearings were made thicker to compensate that are always in contact and make those thicker, compensating for any offsets within the mechanism.
Developing the robot base
The warehouse environment is extremely busy with staff and machinery constantly moving stock around. To effectively manoeuvre the tower within this environment requires a driving platform that quickly understands and reacts to its surroundings.
‘The tower module is mounted to a base which is an autonomous mobile robot,’ says Bushell. ‘This driving platform houses the wheels, batteries, perception equipment, computers and other electronics. It has a completely opposite design philosophy to the tower. The tower needs to be as lightweight as possible to lift to the necessary heights, whereas the base needs to be heavy and robust to provide a stable platform.’
The base consists of a steel and aluminium chassis which houses four lidars, two cameras and a variety of other perception sensors. To achieve complete bidirectionality, two castor wheels are located at the front, two driven wheels in the centre and two at the rear. This arrangement allows the robot to turn through 360 degrees on the spot and therefore the software doesn’t have to account for any turning circles when calculating trajectories.
Another challenge was designing the base to keep the cameras on the tower level whilst the robot moves over uneven warehouse floors. ‘If the robot comes across an obstacle that is, let’s say, 1 cm big, it will cause an offset angle of 1° which equates to a 20 cm horizontal misalignment at the highest camera on the tower – affecting imaging accuracy,’ explains Bushell.
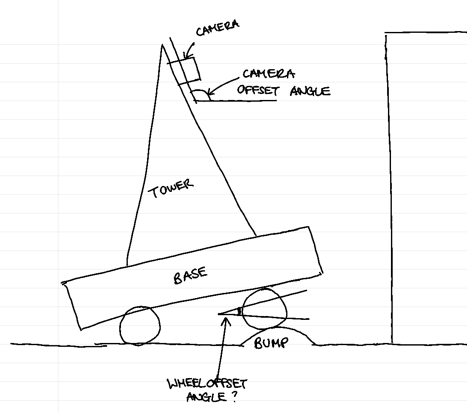
The slightest offset of the base can cause significant inaccuracies for the cameras at the top of the tower. This is why the base has been designed to be stable and cope with undulations of the floor.
‘Consequently, we needed a system which would allow a degree of compliance between the wheels and the base,’ continues Bushell. ‘A suspension system could translate high-frequency vibrations to the tower, while a fully locked system could send severe jolts up the tower. So, we decided to mount each pair of wheels on a pivoting arm system, allowing extra degrees of freedom and providing the leverage necessary to cope with any undulations in the floor.’
Powering a warehouse inventory robot
To provide power to the robot, multiple rechargeable batteries are used. Fully charged, this gives the robot a range of around 4 to 5 hours of scanning time with a recharge period less than 3 hours, making it capable of scanning very large warehouses up to 100,000 pallets in a single day. When the batteries are running low, the robot pauses scanning and travels back to its dock. Once recharged, the robot returns to its last location and continues scanning, ensuring that data from the entire warehouse is captured.
However, to increase the robot’s range, Dexory continue to boost the number of batteries within the base as well as reduce the energy consumption of all its devices. ‘It’s a fine balance between increasing battery capacity and reducing energy consumption,’ says Bushell. ‘Increasing the number of batteries will increase the robot’s range, but if we design it to scan faster, we can capture more information within that runtime.'
'Unfortunately, this consumes more energy which could then overall decrease this runtime. So, we focus on optimising the energy consumption of every device on the robot as ultimately, we want the robot to run for as long as possible and recharge in the shortest time possible.’
The potential of robotic inventory management
The impressive capabilities of the sliding tower structure, along with the agility of the base is only made possible through ingenious mechanical design. As with any pioneering technology, new technical problems arise that have never been solved before. Yet, the innovative approach and resourcefulness of Dexory’s engineers, combined with the relentless compliance with core design principles has helped to develop a truly revolutionary warehouse management system.
‘The fact that there is nothing like this on the market is probably what made developing this robot so challenging,’ concludes Bushell. ‘By not having any existing products to analyse, we were forced to think outside the box which is what led us to such abstract concepts. But the result is a fully autonomous robot that can scan 100,000 pallets in warehouses that are more than 1,000,000 sqft in a single day.’
References
[1] 2023. Global Freight Transport Statistics: International, Europe, and Germany [Online]. DHL.
[2] 2021. The size and make-up of the UK warehousing sector – 2021 [Online]. UKWA.