Daily vs. Yearly: Why automated inventory counts are crucial for your warehouse operations
July 22, 2024
Accuracy and efficiency of inventory management can make or break a business.
Traditionally, inventory counts were conducted manually on a periodic basis—weekly, monthly, or even yearly. However, with advancements in technology, automated inventory cycle counting has emerged as a disruptive solution for the industry.
The pitfalls of manual inventory counting
Manual inventory counting has long been the norm in warehouses and distribution centres. However, it comes with inherent challenges and limitations. Counting large volumes of stock manually is time-consuming and prone to human error.
According to research, manual counting typically results in an accuracy rate of around 65% to 70%, leaving significant room for discrepancies that can impact operations and customer satisfaction.
The role of robotics in automated inventory counting
Robotics plays a pivotal role in automating inventory cycle counting processes. Autonomous mobile robots (AMRs) equipped with sensors can navigate warehouse aisles, scan barcodes, and update inventory records seamlessly. These robots integrate with cloud-based inventory management systems that provide real-time updates and analytics, offering unparalleled visibility and control over warehouse operations.
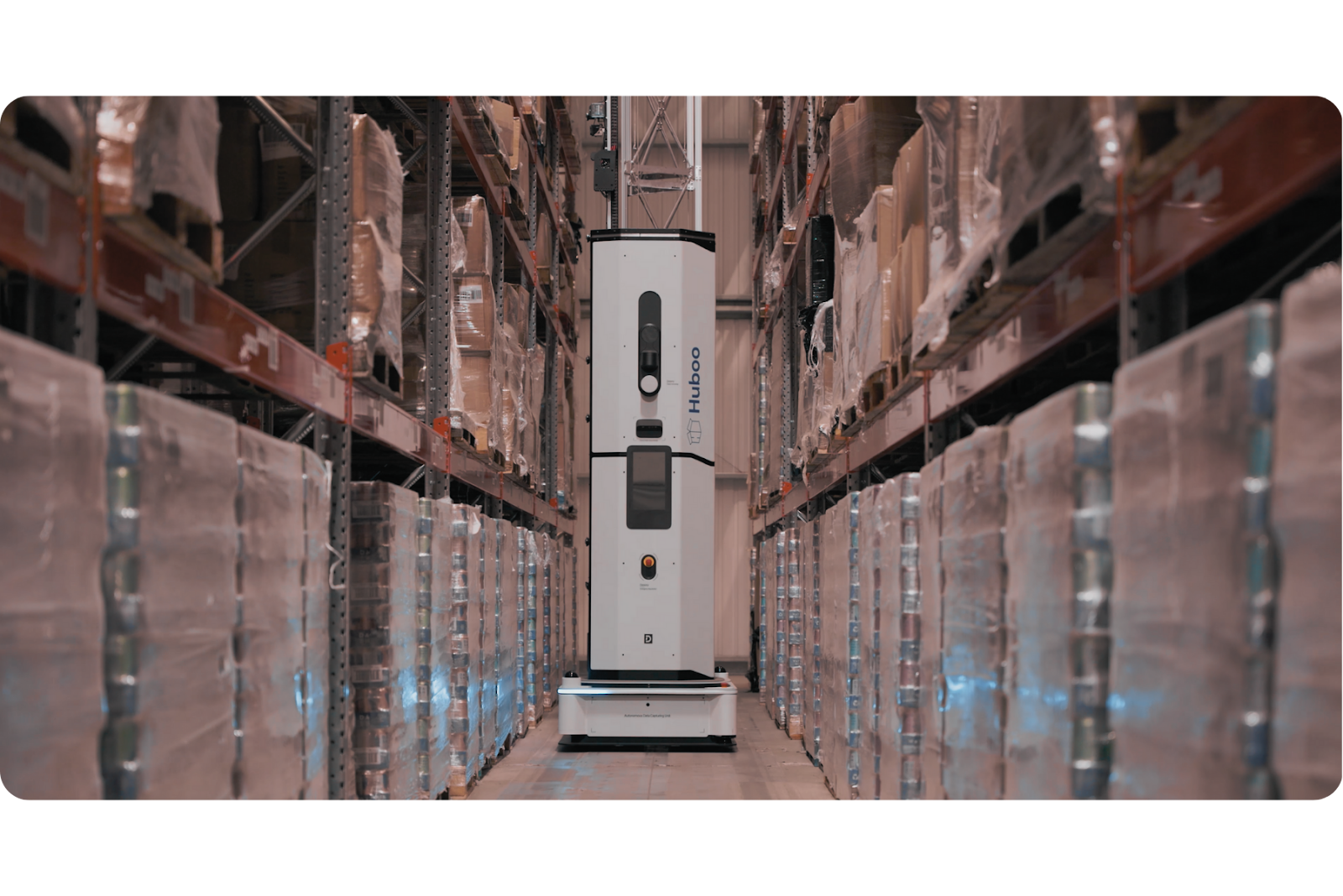
Automated solutions: Why daily inventory counting matters
Improved accuracy and real-time insights
Automated inventory counting, enabled by robotics and AI, offers unparalleled accuracy levels, often reaching 99.9%. By conducting daily counts, businesses can maintain real-time visibility into their inventory levels, reducing the risk of stockouts or overstocking. This timely data empowers decision-makers to optimise stocking levels, streamline operations, and respond swiftly to changing market demands.
Enhanced operational efficiency
With automated systems like DexoryView, warehouses can scan vast areas and thousands of locations within hours, collecting data continuously. This efficiency not only saves time but also enables resources to be redeployed from manual counting tasks to more strategic activities. By minimising the need for manual intervention, businesses can achieve higher productivity and operational resilience.
Real-time data provided by automated systems also empowers logistics managers to make timely adjustments to inventory levels, respond swiftly to market trends, and optimise supply chain processes.
Cost reduction and waste minimisation
Daily inventory counting helps in identifying discrepancies promptly, minimising stock loss, and reducing financial waste. By pinpointing issues such as misplacements or picking errors early on, businesses can optimise their inventory management processes, lower operational costs, and enhance profitability.
While there is a perception that implementing automated systems entails significant upfront costs, the reality often proves otherwise, especially with innovative subscription models now available. These models allow businesses to adopt automated inventory solutions without the need for a large initial investment.
Implementing automated solutions in our warehouse
Implementing automated inventory counting solutions requires careful planning and integration with existing warehouse management systems (WMS). Fortunately, advancements in technology have streamlined this process, allowing new automated technologies to easily integrate with WMS. Data collected through automated inventory systems is fed directly into the WMS, enabling real-time updates and immediate action on any discrepancies identified during daily inventory counts.
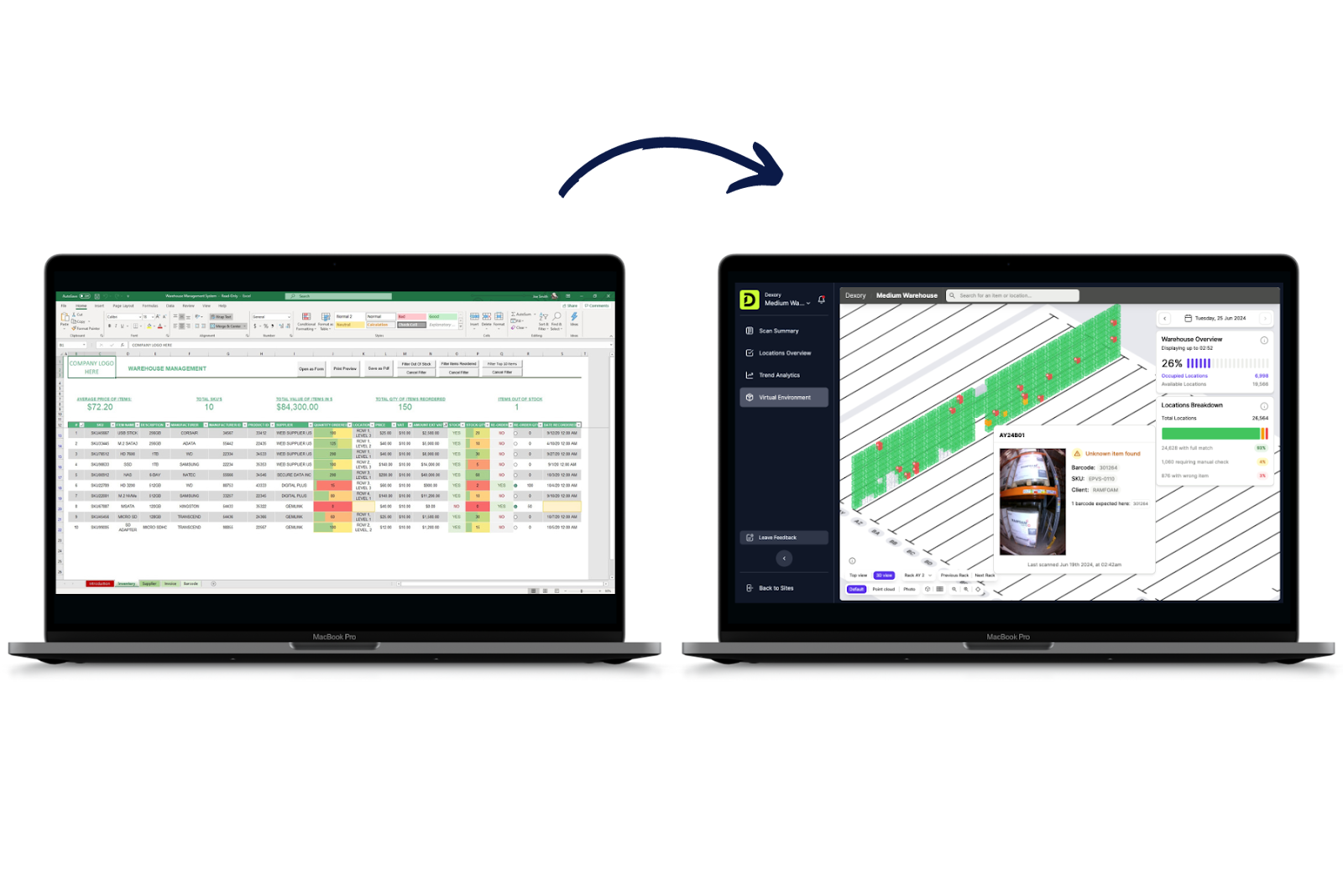
Conclusion
In conclusion, automated inventory cycle counting represents a key shift in the logistics and warehousing industry. By moving away from traditional manual daily or weekly cycle counts and periodic counting methods towards daily full site automated inventory processes, businesses can achieve greater accuracy, efficiency, and agility in managing their inventory.
Close your Visibility Gap: Download our paper to explore solutions for a more resilient and efficient supply chain