Automated inventory management: The benefits go far beyond stock accuracy
May 7, 2025
When businesses consider automated inventory management, the first benefit that usually comes to mind is improved stock accuracy, and for good reason. Knowing exactly what’s in your warehouse, at any time, is the foundation of efficient operations.
But here’s the truth: inventory automation is about much more than just accuracy. The right system doesn’t just track stock, it transforms your operations, frees up your team, and drives serious cost savings. And as warehouses get larger, SKUs multiply, and supply chains become more complex, manual inventory tracking simply can’t keep up.
In this article, we’ll explore the core benefits of automated inventory management, highlighting why it’s quickly becoming a must-have, not a nice-to-have, for modern logistics and supply chain teams.
1. Real-time visibility across your entire operation
Unlike manual checks or periodic cycle counts, automated inventory systems capture data continuously. This means you’re no longer working with outdated figures or second-guessing stock levels.
Real-time visibility allows you to:
- Know your current stock position across every location, aisle, or bin.
- Identify discrepancies instantly and take corrective action before they snowball.
- React quickly to low stock levels or anomalies.
This level of visibility has a direct impact on fulfilment speed, replenishment accuracy, and customer satisfaction. It turns your inventory data into a live dashboard of your operations, helping you move from reactive to proactive management.
Real-time visibility leads to real-time decisions. And that’s a game changer.
2. Faster, safer, and more efficient processes
Stock checks, cycle counts, and replenishment planning are traditionally time-consuming and error-prone tasks. Automation fundamentally changes the speed and safety of these operations.
Benefits include:
- Cycle counting completed in hours instead of days.
- No need for scissor lifts or forklifts to scan high shelves.
- Inventory scans during active shifts with no aisle shutdowns.
- 24/7 operation capability.
Not only do these capabilities lead to significant time savings, but they also reduce the risk of workplace injuries and minimise operational disruption. The result? A smoother, safer, and more productive warehouse floor.
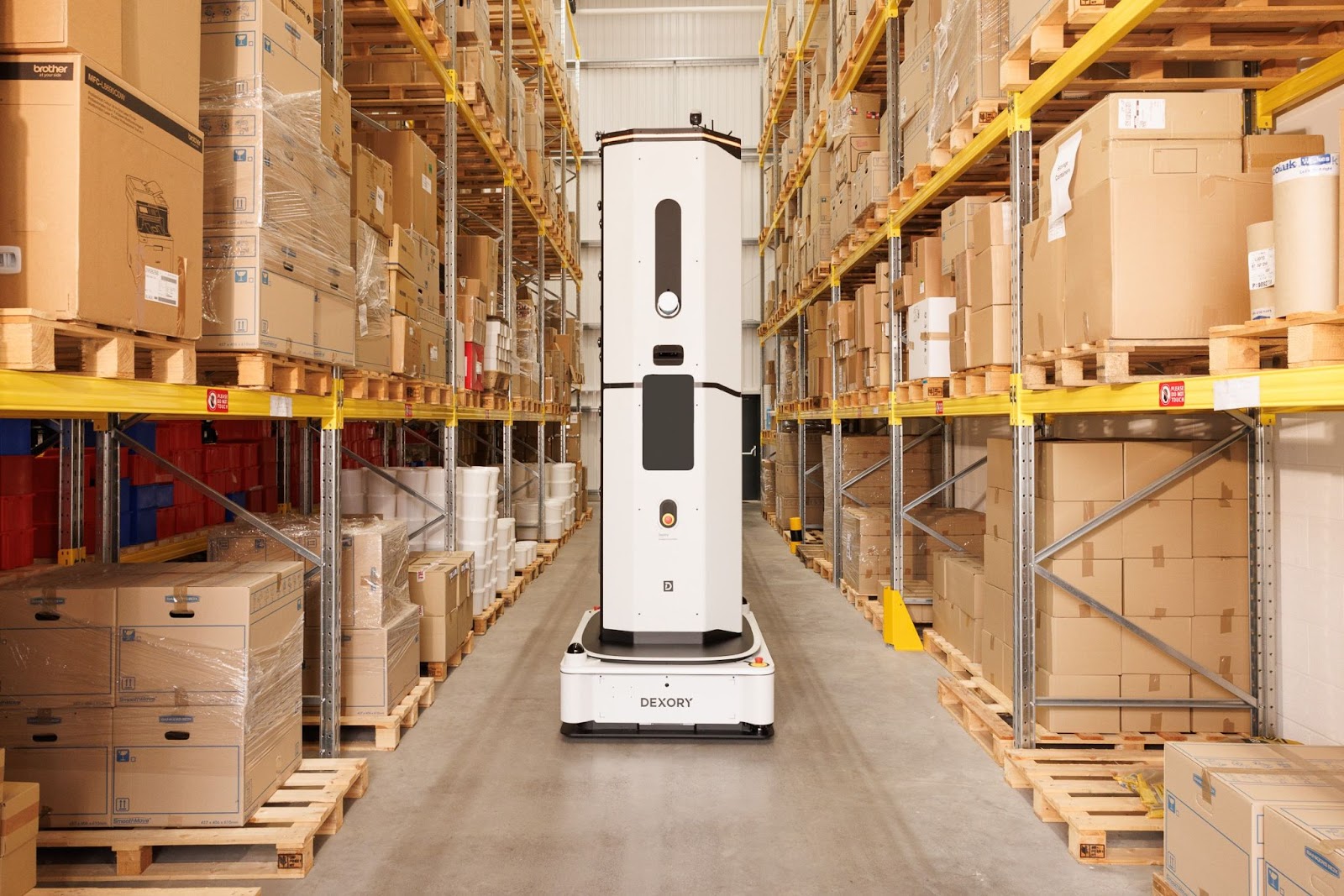
3. Predictive insights that support better planning
One of the biggest shifts with automated inventory management is the move from hindsight to foresight. Manual processes tell you what did happen. Automated systems tell you what is happening and, increasingly, what will happen.
With a constant stream of data, you can:
- Identify slow-moving stock and optimise reorder points.
- Detect seasonal trends and adjust purchasing strategies accordingly.
- Reduce excess stock and improve cash flow.
Layer in AI-powered analytics, and your inventory system becomes a forecasting tool that supports better planning across procurement, logistics, and even marketing.
You don’t just see what’s happening, you understand why it’s happening, and what to do next.
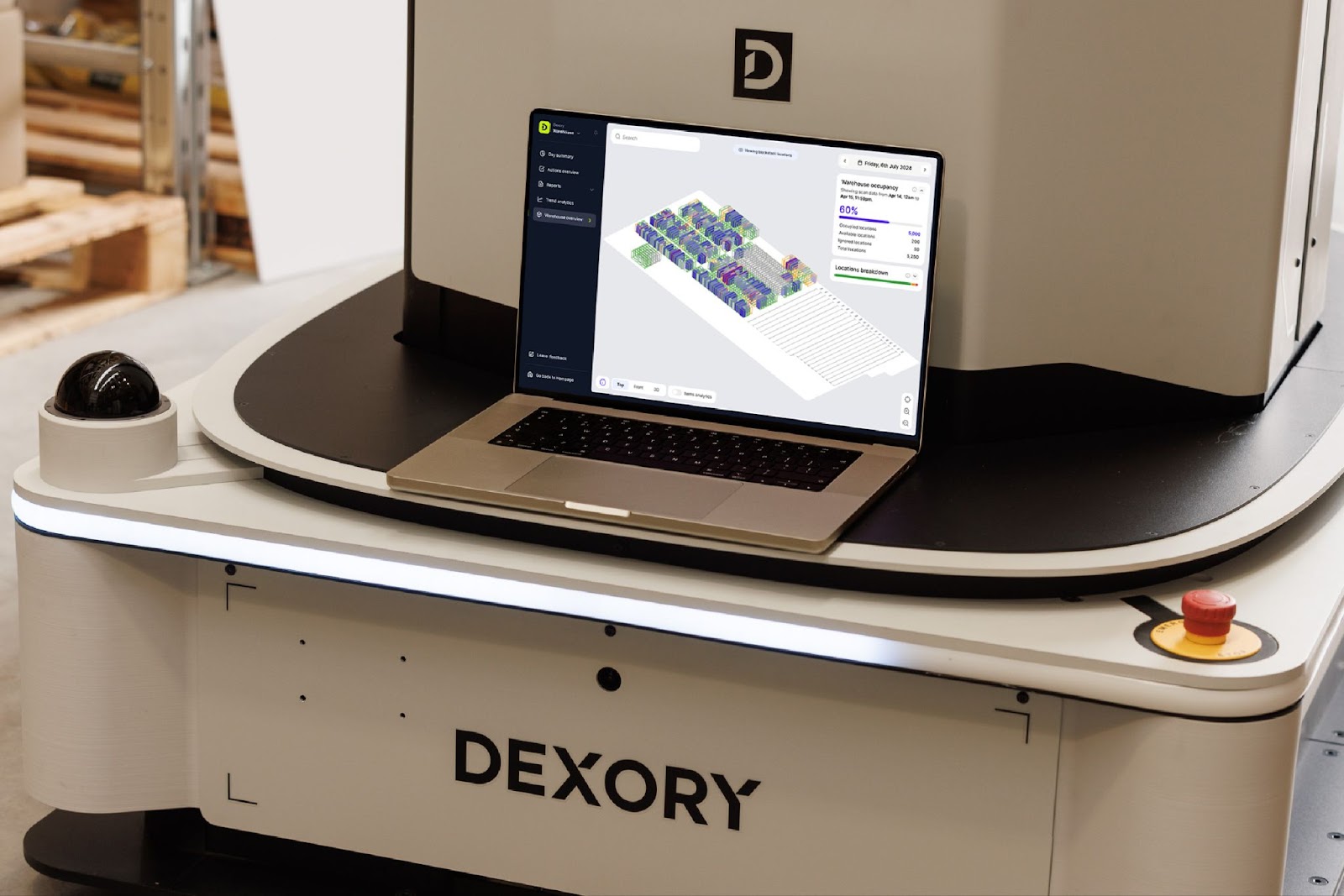
4. Enhanced workforce productivity and morale
Manual inventory management often involves repetitive, physically demanding tasks like climbing ladders, scanning boxes, or cross-checking paperwork. This not only increases the risk of error but also contributes to low morale and high turnover.
Automation changes the role of the warehouse worker:
- Teams are freed from monotonous data collection.
- Staff can be reallocated to value-adding or customer-facing tasks.
- Upskilling opportunities open up as employees learn to manage and interpret automated systems.
Rather than replacing jobs, automation enables people to do more meaningful, impactful work. It reduces burnout, improves job satisfaction, and contributes to a safer, more resilient workforce.
5. Scalability without complexity
As your business grows, so does the complexity of your inventory. More SKUs, more locations, more movement. Manual tracking doesn’t scale easily, it becomes a liability.
Automated inventory systems make growth manageable by offering:
- Seamless onboarding of new warehouses, zones, or products.
- Standardised data across multiple sites.
- Centralised monitoring and reporting.
Whether you’re expanding into new geographies or simply adding new product lines, automation provides the agility and control you need to scale without the headaches.
Scaling your business shouldn’t require scaling your inventory problems.
6. Lower costs and a faster ROI
Inventory automation is more than a technology investment, it’s a financial strategy. Businesses that adopt automated inventory management often report measurable ROI within months.
Here’s why:
- Reduced write-offs from misplaced or expired inventory.
- Fewer stockouts and overstock situations.
- Lower labour costs through reduced manual processes.
- Improved order accuracy and customer retention.
Some businesses even avoid costly infrastructure investments altogether, thanks to space optimisation and more accurate inventory turnover data.
The cost of inaction is rising. Automation is doing more, but it’s also about spending less to achieve better results.
The cost of inaction is rising. Automation isn’t just about doing more — it’s about spending less to achieve better results.
Want to see the impact in action?
Watch how Iron Mountain achieved significant time and cost savings through automation in our joint webinar:
Explore how Dexory delivers a 219% ROI over 3 years and a payback period under 6 months in our Forrester Total Economic Impact™ study, based on real customer results.
7. Seamless integration with existing systems
A concern for many operations teams is whether automation will disrupt existing workflows. Modern inventory management platforms are built to integrate seamlessly with:
- Warehouse Management Systems (WMS)
- Enterprise Resource Planning (ERP) software
- E-commerce and retail platforms
- Shipping and logistics providers
This ensures a smooth data flow across systems, enhancing end-to-end visibility and enabling coordinated decision-making across the entire supply chain.
8. Improved customer satisfaction
Ultimately, the goal of any supply chain operation is to deliver the right product, to the right place, at the right time. Automated inventory management contributes directly to this by:
- Reducing order errors.
- Speeding up fulfilment.
- Providing accurate delivery updates.
Satisfied customers are more likely to return and recommend your business. In competitive markets, that edge is crucial.
Final thoughts: It’s about more than just knowing what’s in stock
Stock accuracy may be the spark that gets people thinking about automation. But it’s the broader operational, financial, and strategic benefits that make automated inventory management such a powerful tool for the modern warehouse.
From reducing labour costs and improving safety, to enhancing forecasting and enabling scalability, automation is becoming a cornerstone of smart logistics strategies. And as supply chains become more dynamic and demand more visibility, real-time control is essential.
If you’re still relying on spreadsheets, manual scans, or outdated systems, now is the time to explore the possibilities of automation. Because in today’s logistics landscape, speed, agility, and insight are your most valuable assets.
Looking to take the next step?
Explore how Dexory’s fully automated inventory solutions help warehouses around the world boost productivity, improve stock visibility, and unlock significant ROI, all with zero disruption to operations.
Get in touch today to see it in action